Design of a Face Mask Disposal Process
|
 |
|
|
|
A team of Professional Doctorate in Engineering (PDEng) trainees of the Process and Equipment Design programme at TU Delft has designed a process to convert face mask waste into mainly polypropylene pellets, an intermediate product for the plastic industry. This process is economically and environmentally attractive as it has a Pay-Out Time of less than 1.5 year and it reduces CO2 emissions by over 90% compared to incineration, which is the common practice for face mask waste disposal.
Project Background: The Increasing of Face Mask Waste
Due to unprecedented conditions caused by the spread of the COVID-19 virus, the usage of medical face masks has dramatically increased, it is estimated that 10 million per day are used in The Netherlands. This waste is currently incinerated or disposed in the environment, leading to a loss of potential resources and CO2 emissions.
A mixed surgical and respiratory face mask stream presents an average material composition of about 80 wt.% polypropylene (PP), 10 wt.% aluminium, 2 wt.% iron and 8 wt.% of other polymers is considered. This stream can be recovered and recycled into commercial products, leading to a more circular solution. The design aims to safely recover 80% of the materials in the face mask waste stream (10 tons/day) in a technically and economically feasible way, with a minimum Technological Readiness Level (TRL) of 6 and a Pay-Out Time (POT) lower than 1.5 years.
The production of polypropylene pellets is selected as the most suitable disposal solution based on technical, economic and market feasibility analysis among other possible processes such as pyrolysis (to produce fuels), production of mixed shredded plastics (to be used as asphalt binders), and production of nonwoven and woven polypropylene fabric.
The Solution: Polypropylene Pellets Production
The designed process with capacity of 10 tons per day of mixed medical masks per day composes of face masks ‘quarantining’ in a warehouse to ensure virus deactivation, masks shredding into small flakes and mechanical separation of PP cloth components. The PP flakes are then extruded to produce pellets, which can be sold to plastic manufacturers to produce various PP-based products (e.g., plastic containers, bins, cable insulation, packaging). The discarded flakes are further separated into aluminium and iron components, which can be sold as scrap metals.
The process achieves a remarkable material recovery of 88 %, which means that from the feedstock 2500 tons/y of PP pellets is produced and 400 t/y of scrap metal is recovered. Moreover, it provides environmental benefits compared to incineration, reducing both CO2 emissions and solid waste production by 90%. The economic potential is also comparable to incineration, considering an investment of 1.7 M€ and a Pay-Out Time of lower than 1 year.
The Challenges and Opportunities
The designed process to produce recycled PP pellets from face mask waste represents an environment-friendly and economically attractive disposal solution. The process relies on the continuous supply of separately collected face masks from healthcare facilities and public places. However, a separate collection process does not currently exist and it could require a minimum investment of 1 Million Euro.
According to recent news, in the midst of the pandemic the Dutch Governmental Organisations purchased a large access of face masks, resulting an approximately 2 billion of excessed face masks[1]. Due to their limited shelf life, most likely they are to be disposed. Therefore, the designed process can be implemented to tackle this problem in a more circular way than incineration.
The PDEng Team
The PDEng team of Process and Equipment Design, who started the programme in February 2020, consists of five people: Ana Carolina, Ezgi, Federico, Silvia and Tamoor.
The diversity of the team with different nationalities (Portugal, Turkey, Italy and Pakistan) and backgrounds (Chemical, Energy and Mechanical Engineering) helped them to successfully overcome the challenges through their first year. After having finalised their Group Design Project, the five trainees will complete the PDEng programme with a one-year Individual Design Project.
[1] https://www.telegraaf.nl/nieuws/1370393510/ministerie-komt-om-in-2-miljard-mondkapjes-spatschermen-en-handschoenen
|
|
|
|
 |
|
|
For more information about the project, please contact the program coordinator: m.hajivandi@tudelft.nl
If interested in the PDEng program, please visit the TUDelft website and the official website of the PDEng Employees Association (DIDEA).
The present project was financed by HELIS Academy , part of Interreg (the European Fund for Regional Development) aiming to increase high-tech cooperation offering training, internships and traineeships in the Life Sciences and Health sector..
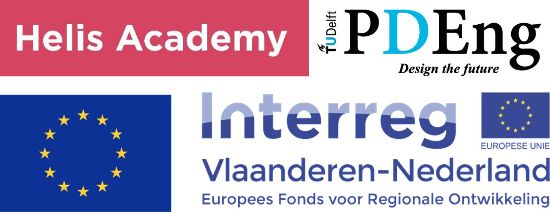 |
|
|
|
 |
|
|